MVR技術在化工廢水處理領域的應用案例分析
來源:本站日期:2019-08-15 01:24:11 瀏覽:3714
項目名稱:MVR技術在河北精細化工行業廢水處理案例中的應用
蒸發器類型:MVR蒸發器
設備規格:處理量3t/h
項目概述:
客戶公司為河北廊坊的精細化工企業,該公司主要生產硅酸鋁,此次處理物料為硅酸鋁的生產廢水。本系統的設計處理對象為3t/h含硫酸鈉、氯化鈉鹽廢水。采用了MVR蒸發技術工藝,MVR技術在節能降耗方面頗具優勢。
水質情況分析:
客戶所要處理的物料主要成分為氯化鈉、硫酸鈉鹽。康景輝技術部水質測試組對客戶水質進行測試,根據原水水樣濃度、氯離子濃度、原水COD、原水PH值、原水鈉離子濃度、原水鈣離子濃度等進行技術分析測試,針對所測得水質實驗數據進行蒸發工藝技術選型。
物料成分中除了氯化鈉、硫酸鈉鹽,還含少量COD(化學需氧量):182mg/L,鈣離子:58.4mg/L,PH:7。
工藝技術設計分析:
由于該化工企業的含鹽廢水成分復雜,無法使用單一方式一步處理,因此康景輝根據廢水中含鹽量和有機物濃度的不同,考慮到后期的運行成本,推薦系統選用MVR蒸發技術處理該廢水,又由于該廢水濃度提高后如果不攪動很容易掛壁,所以考慮采用采用組合工藝,利用MVR技術與強制循環技術相結合的工藝模式進行該廢水的處理,即MVR技術+強制循環的組合工藝。
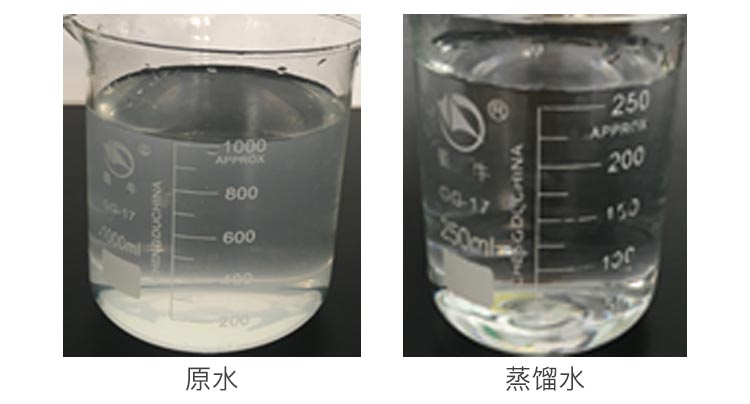
(實驗室進行水質測試分析時的水質對比圖)
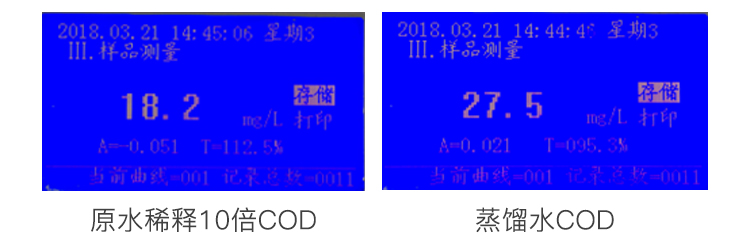
(COD/氨氮測定儀測定處理前后COD含量對比)
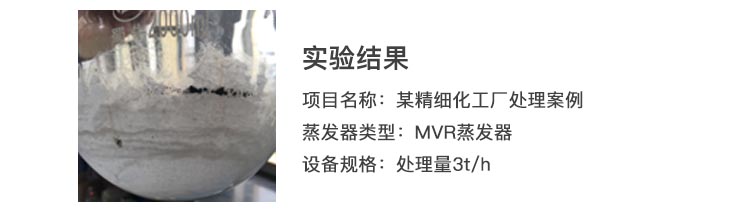
工藝流程描述:
蒸發系統的流程:
物料流程:原水(處理后的原液)→預處理系統→預熱系統→蒸餾水預熱→不凝氣預熱→MVR技術+強制循環工藝蒸發器→出料→離心機→母液回流或者外排(物料離心打包)→固體產出
預熱工藝:處理后的原液經泵至蒸發系統的預熱系統。即:3000kg/h的原液和返回的150kg/h母液首先進入預處理系統,去掉不利于蒸發的鈣離子以及COD等,再進入預熱系統。
首先原液(30℃)通過蒸餾水預熱器與MVR蒸發器排出的高溫冷凝水(112℃)進行預熱,原液預熱到95℃,蒸餾水降溫到40℃ ,換熱后的蒸餾水通過管道輸送至污水處理站進行處理。通過一級預熱后的熱物料再經過不凝氣預熱器與不凝氣(112℃)換熱,進一步回收系統中剩余能量,原液升溫至105℃,不凝氣通過管道輸送至尾氣處理系統。
預熱后的混合液再進入MVR強制循環蒸發器的循環泵的進口,物料經過循環泵的作用,在加熱室吸收蒸汽側的熱量,然后在結晶器沸騰,沸騰蒸發的二次蒸汽上升,濃縮液受重力影響停留在分離器底部。經過蒸發后,分離器的料液濃度上升,物料濃度達到60%,排出分離器,進入稠厚器,再進入離心機,得到的晶體126kg/h排出系統,150kg/h的母液返回系統。
強制循環蒸發結晶工藝:濃縮后的物料經強制循環泵進入強制循環蒸發器,流動過程中受換熱管外壓縮后的蒸汽加熱,物料進入結晶分離器后沸騰蒸發,物料以一定的流速(1.8~2.5m/s)通過加熱管及強制制循環蒸發器保持一定的靜壓,這樣可以有效的緩解強制循環蒸發器換熱管的結垢問題。蒸發產生的二次蒸汽進入分離室,濃縮液停留在結晶分離室內育晶。
結晶分離工藝:待分離器內的結晶物料達到設計要求后,通過晶漿泵排出分離器,進入稠厚器,晶漿上清液通過溢流裝置進入母液罐;稠厚的鹽通過離心機分離出硫酸鈉鹽,離心母液進入母液罐暫存。
母液回流工藝:通過離心和溢流的母液溫度降低,通過母液罐夾套用蒸汽對母液進行預熱,使物料溫度達到 102℃;然后利用母液泵輸送至系統內繼續蒸發結晶; 在蒸發濃縮倍數增大時,可外排部分母液進污水處理站后續處理。
二次蒸汽流程:
二次蒸汽→除霧→加熱器蒸汽側→冷凝→回收熱量→排出系統
蒸發產生的二次蒸汽夾帶有少量的液滴,蒸發產生的二次蒸汽在分離器內以一定的速度上升,進入在分離器內設有特殊結構的除霧裝置,通過逆流洗滌,將二次蒸汽中夾帶的微小液滴洗滌出來,重新進入料液。經過除霧后的二次蒸汽進入壓縮機的進氣口, 經過壓縮機做功,溫度由99.93℃提升到116.05℃,再沿著二次蒸汽出口管道,離開壓縮機出氣口后進入系統主加熱室,釋放潛熱,冷凝成水。
冷凝水進入冷凝水緩沖罐,冷凝水則通過排水泵送往蒸餾水預熱器,降溫釋放熱量給原液,最終冷凝水進入污水處理站。
MVR技術+強制循環技術的優勢:
選用MVR技術是因為該技術節約蒸發成本,使用MVR技術可以節省大量能源消耗,降低運行成本效果可觀,增加相當的經濟效益。
強制循環泵為一大流量低揚程的軸流泵,為強制循環蒸發結晶配套使用,為晶體生長提供足夠的循環速度,有效快速降低溶液過飽和,避免溶液爆發成核,有效提高加熱室管間流速,增大傳熱系數的同時避免物料堵管。
MVR強制循環蒸發器的特點:
1、節能高效、單位能耗低;
2、工藝簡單、實用性強;
3、蒸發速率高、濃縮比重大、抗鹽析、抗結垢、防結焦。
MVR強制循環蒸發器的現場實拍: